Prusa Build
Unexpected side-project time! I’ve been sans-3D-printer for 6 months, which is about 5.5 months too long. Time to change that...
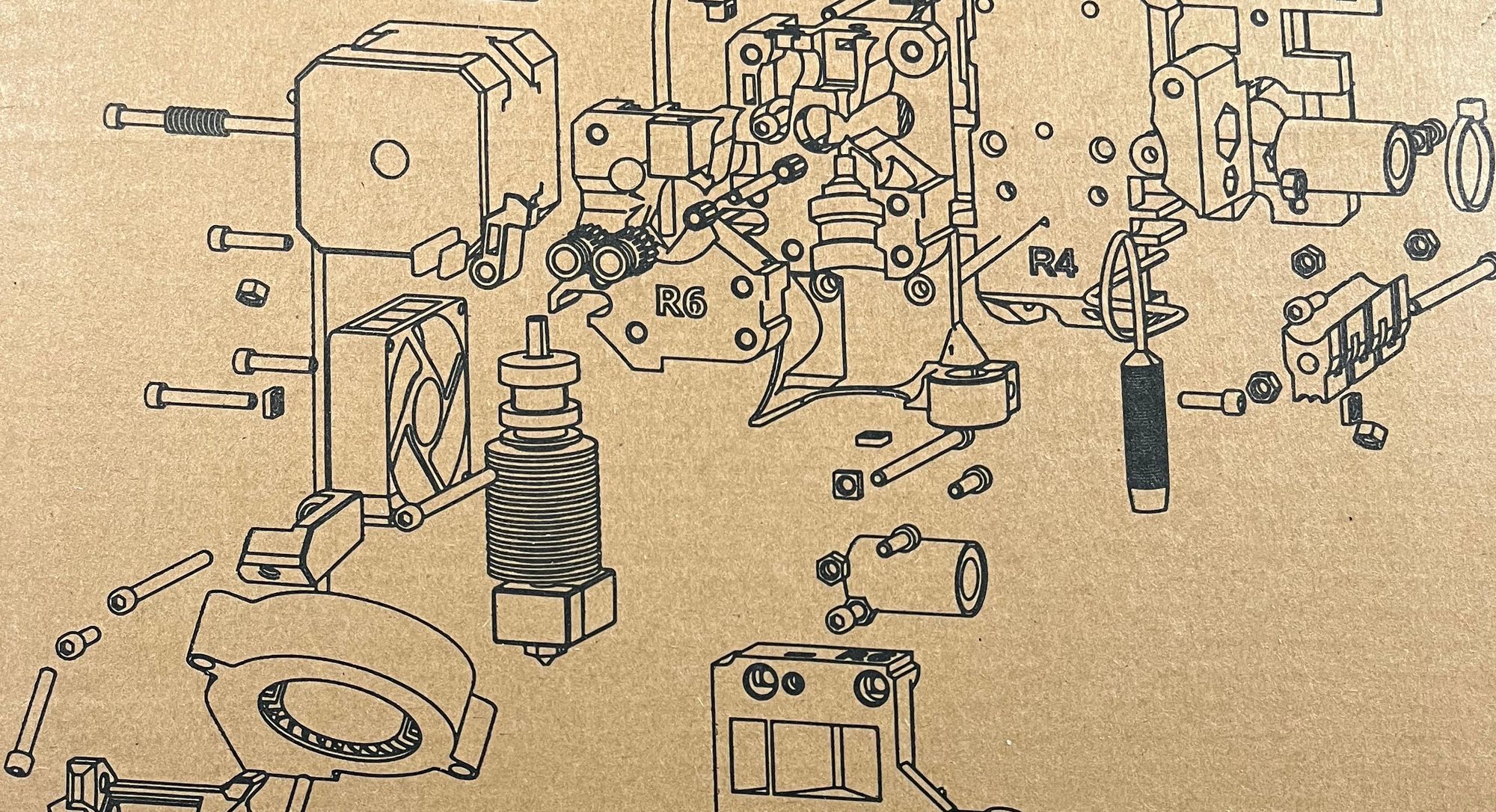
Unexpected side-project time! I’ve been sans-3D-printer for 6 months, which is about 5.5 months too long. After a very intense lap of the forums and review sites, the influencer and influencer-shamer vids, and a re-check of the gut, I decided the Original Prusa i3 MK3S+ was for me. A little too “3D printed” for my tastes, but the Internet had nice things to say. It comes as a “kit”, but what doesn’t these days. Silly me didn’t realise this is no Ikea-style one-allen-key job! I haven’t had this much fine building exercise since my model plane days as a kid. And even that experience is no comparison. So when you go through a journey like this, you feel compelled to share. Talk about viral-survivor-bias marketing!
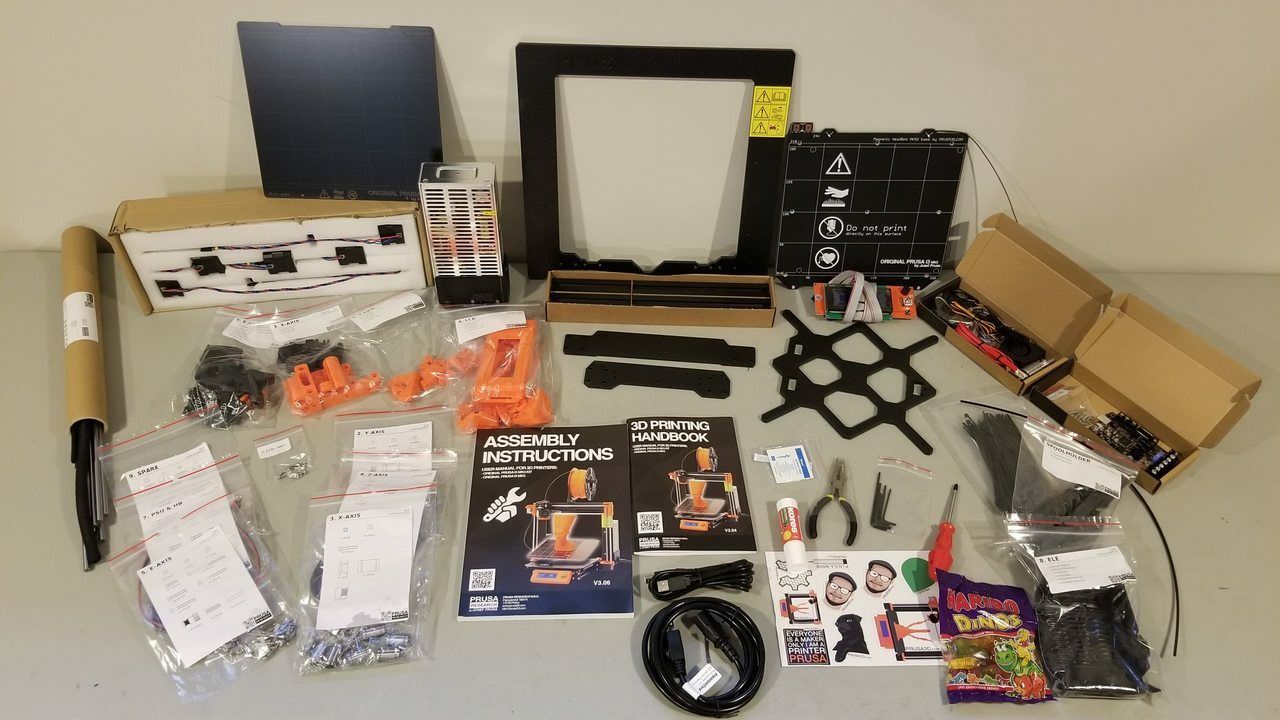
Just assembling the frame took at least 6 hours. These are no ordinary 3D printed parts! It’s stunning that 3D printing has come so far in the last 5 years that this company can have a business designing self-replicating printers, whose parts are such high tolerance and finish quality.
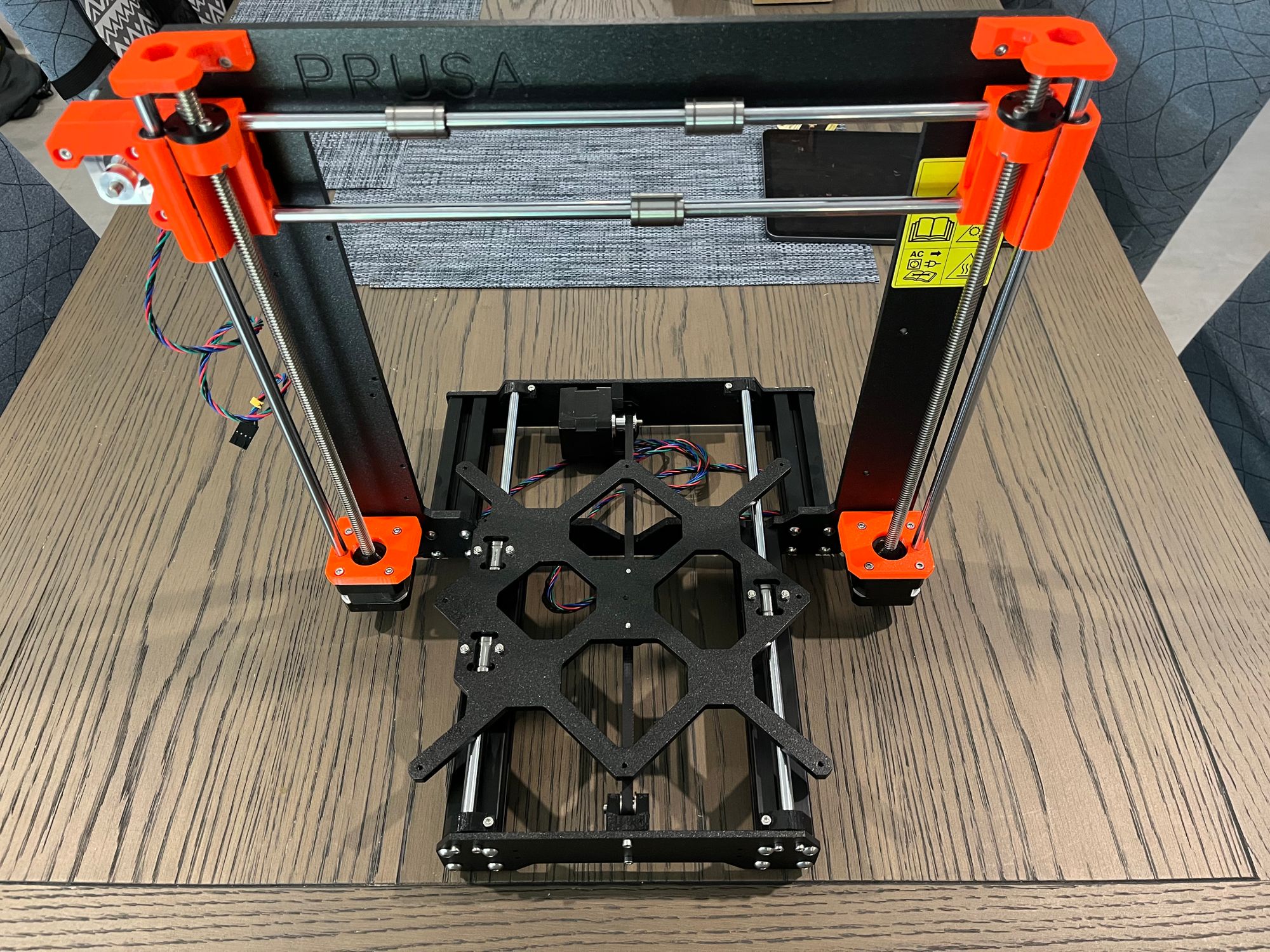
By fantastic coincidence, the extruded aluminium in the subframe is the exact 3030 T-slot profile that I’ve been evaluating for another project. That other project was about to cost me $500 to order some sample materials - suddenly unnecessary, as I got to handle and assess these parts during assembly.
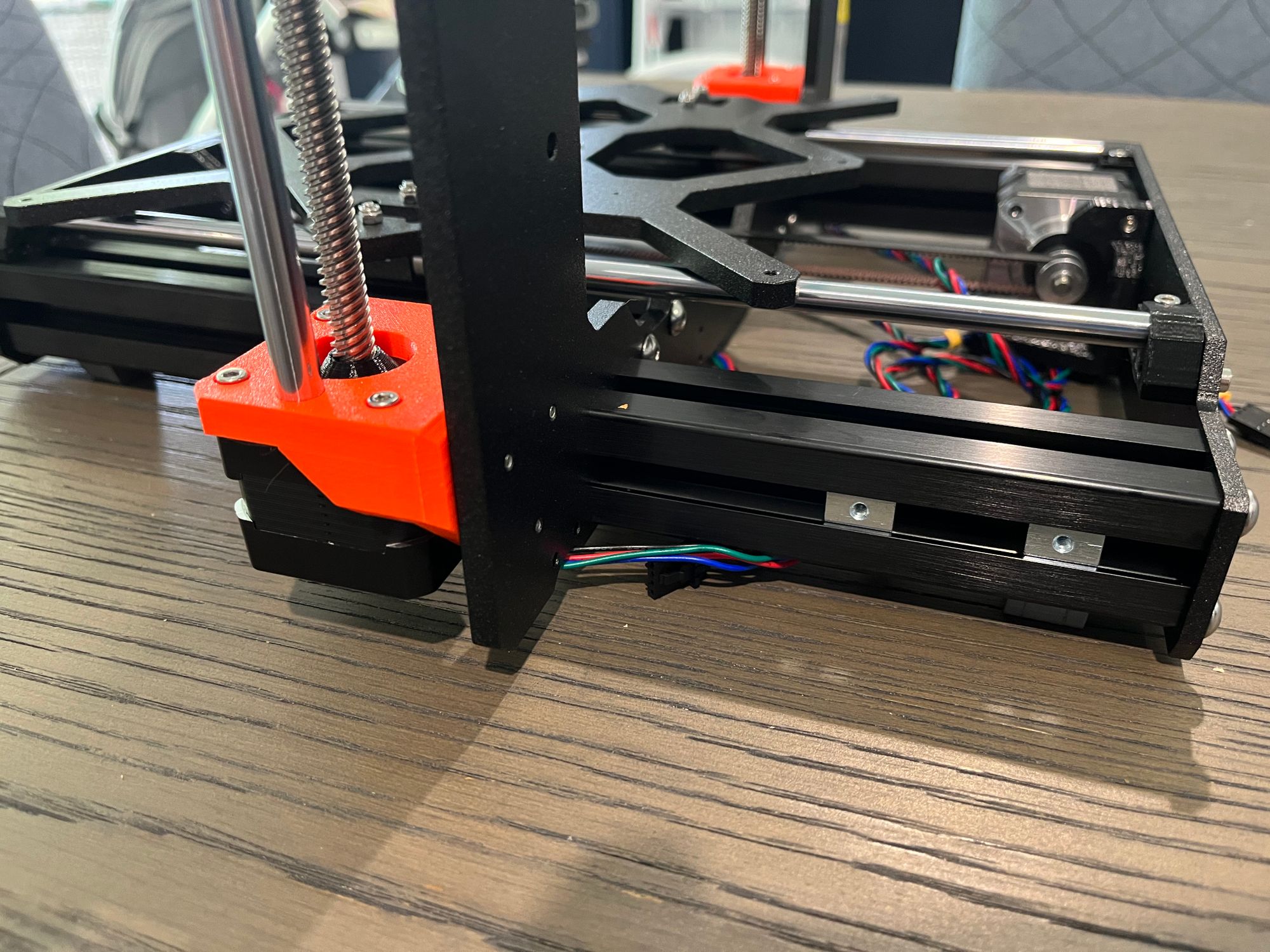
All printed parts come from Prusa’s print farm (and are open source). The farm runs the textured build plate, which I also bought. Pretty handy opportunity to see the effect on printed parts prior to my first print.
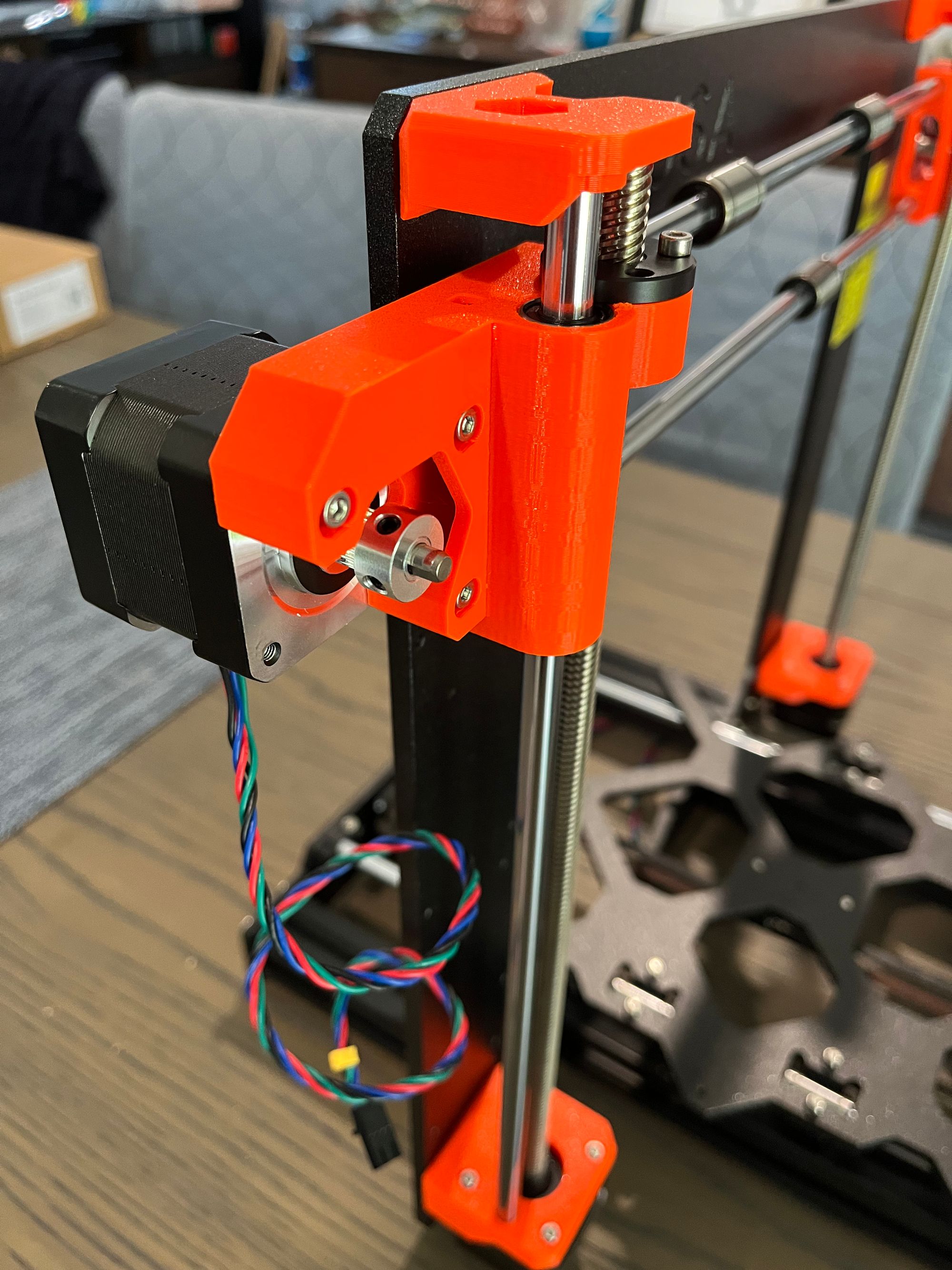
Every assembly chapter comes with its own set of bagged fixing hardware, plastic parts and electronic components. This is chapter 5, the “E-axis” (extruder). The first chapter where the classic plotter frame becomes a printer.
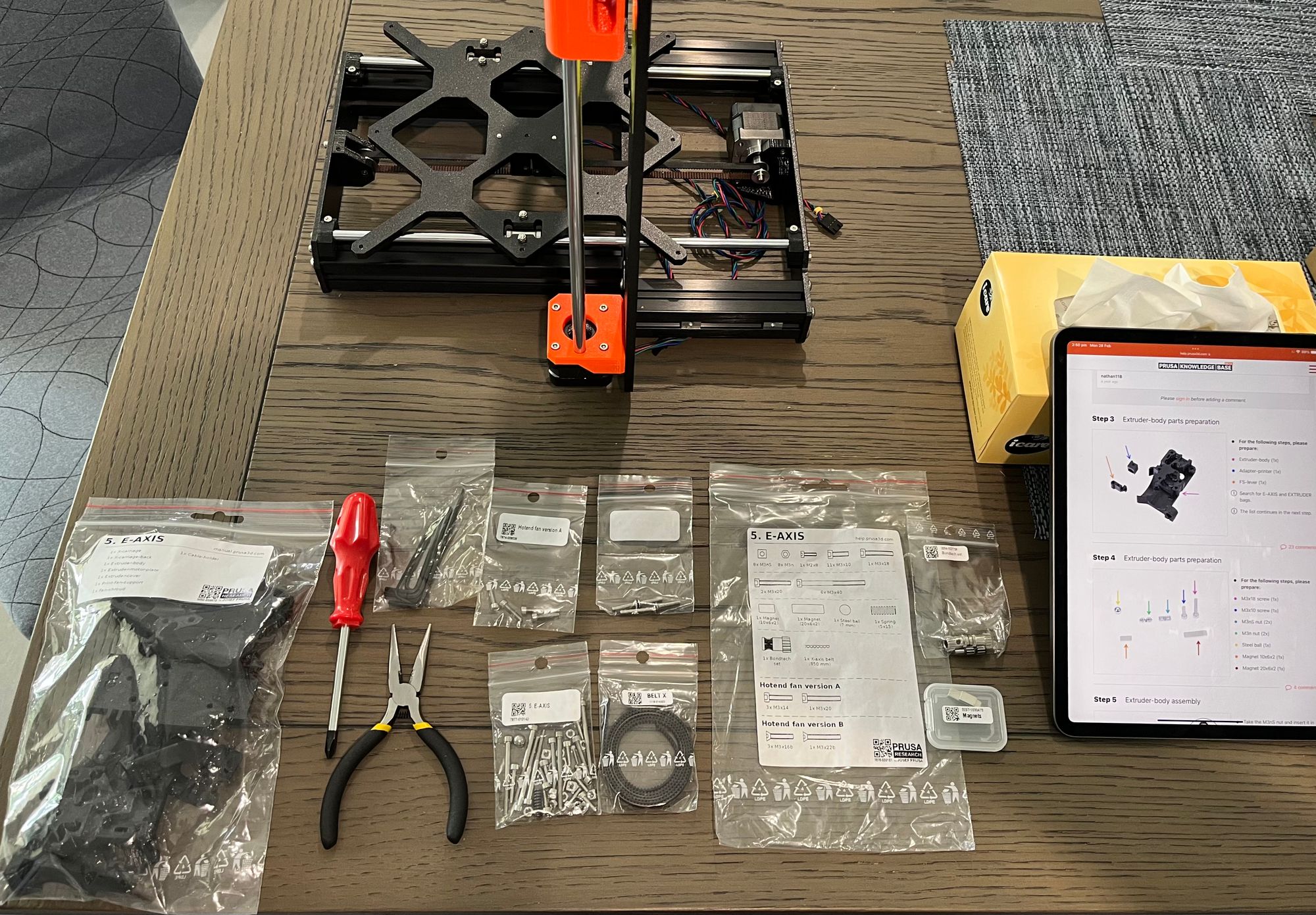
Even the extruder itself is a DIY-assembly job. The confidence in complex printed features is extraordinary. Some of these recesses have teeth, blind passages and interference fit features!
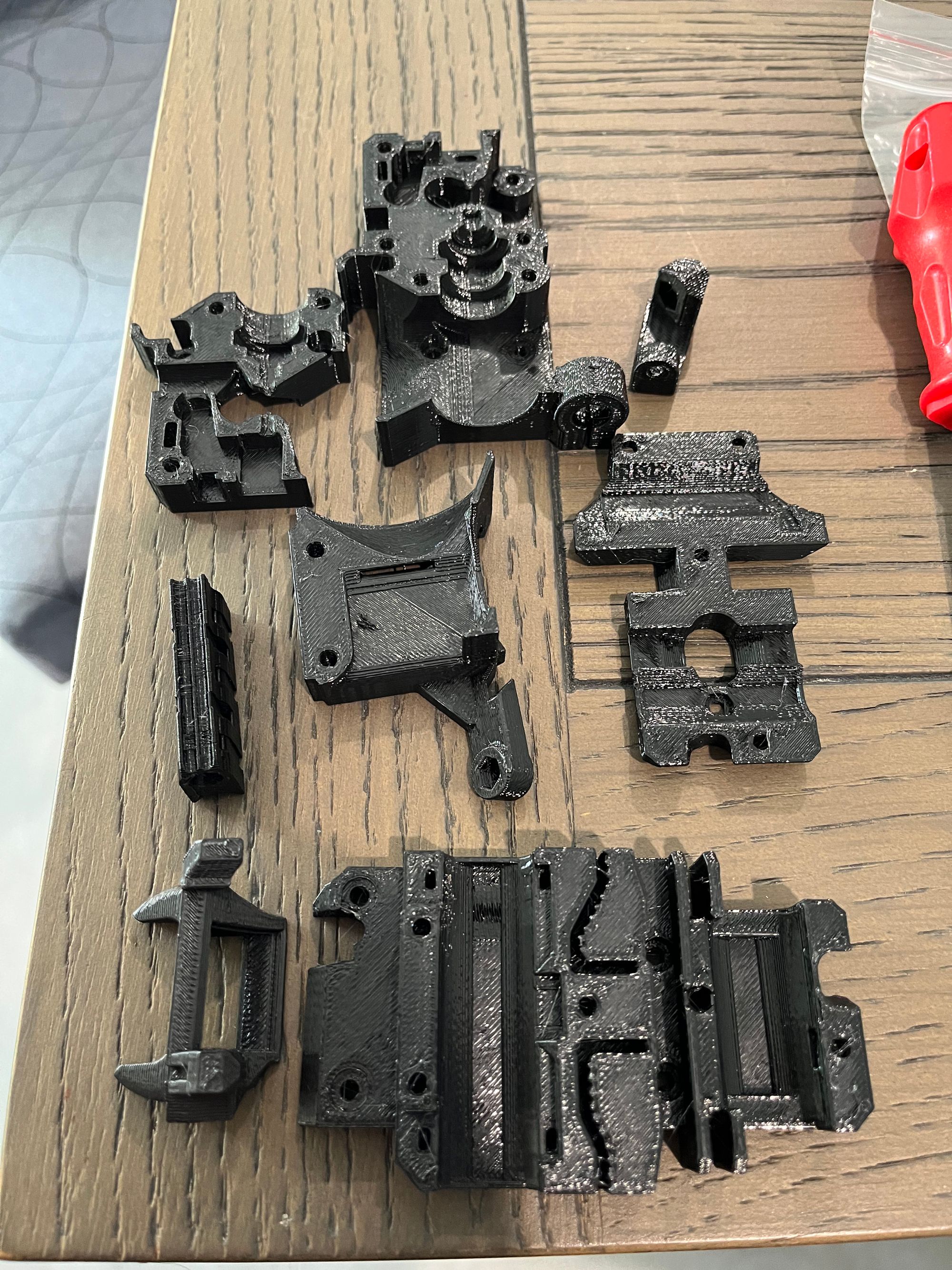
The various graphic design elements are gorgeous, obviously a point of pride amongst the occasionally aesthetics-adverse 3D printing crowd.
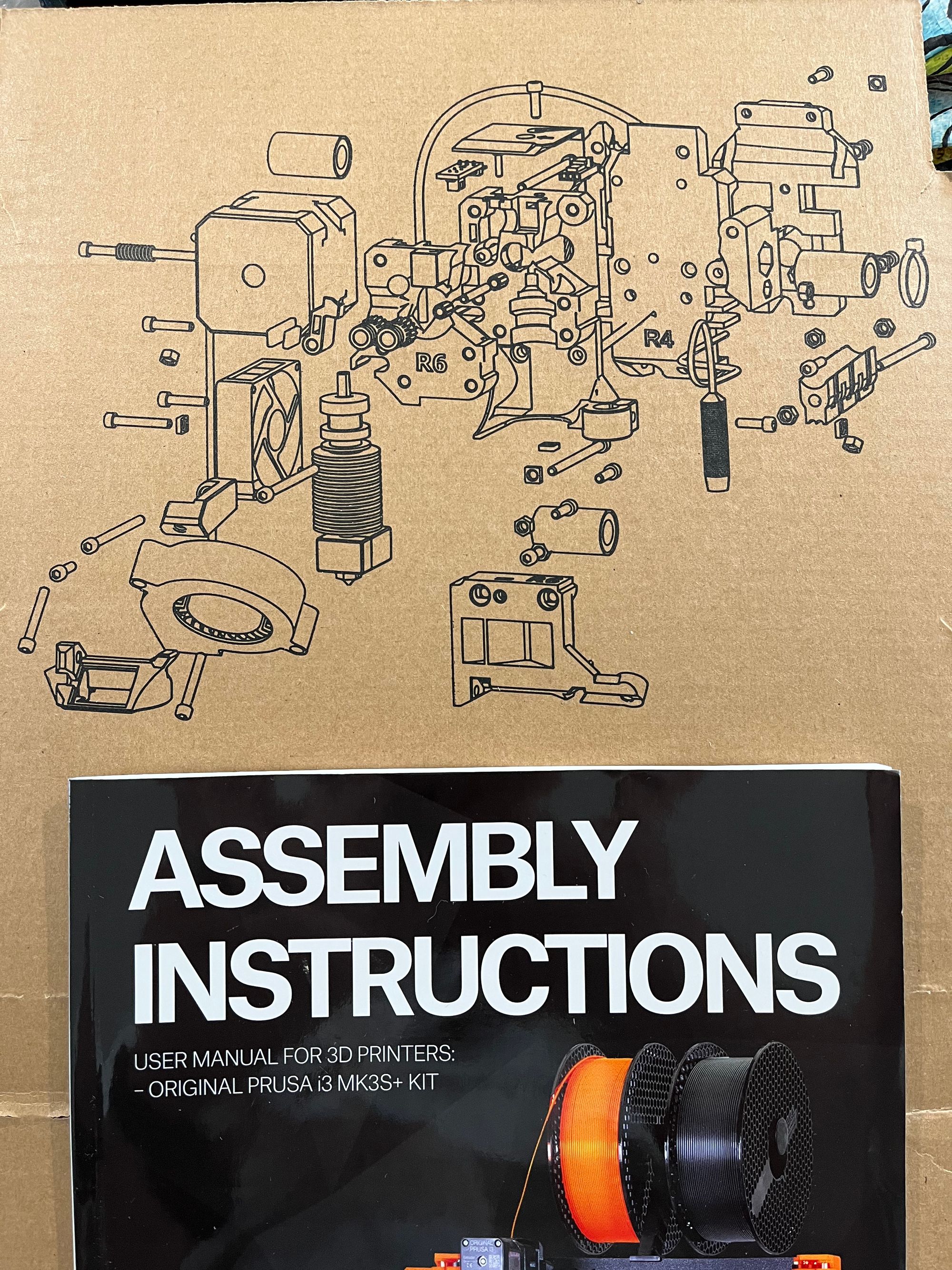
I’m a confident handyman, but some of these assemblies are a feat!
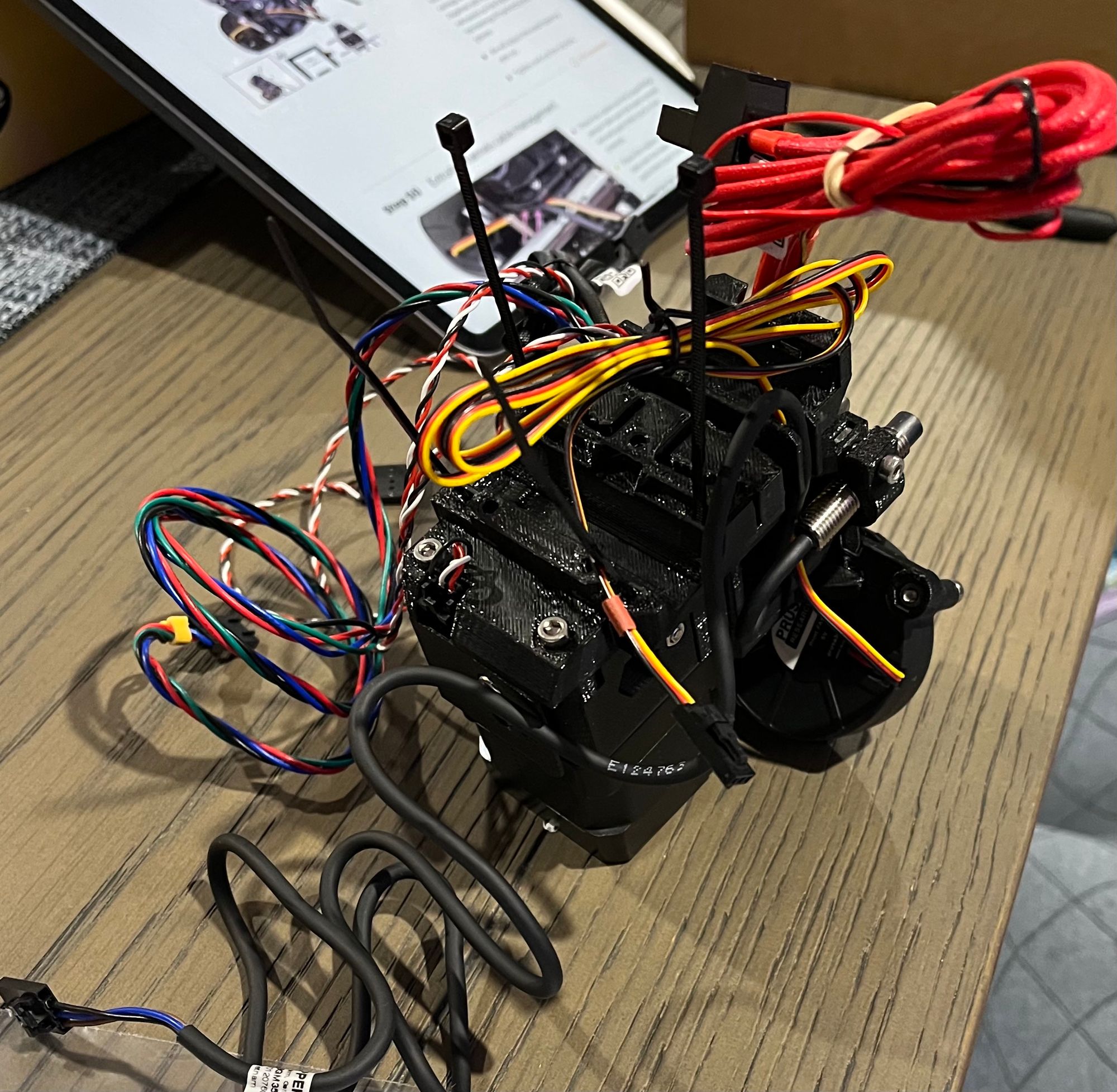
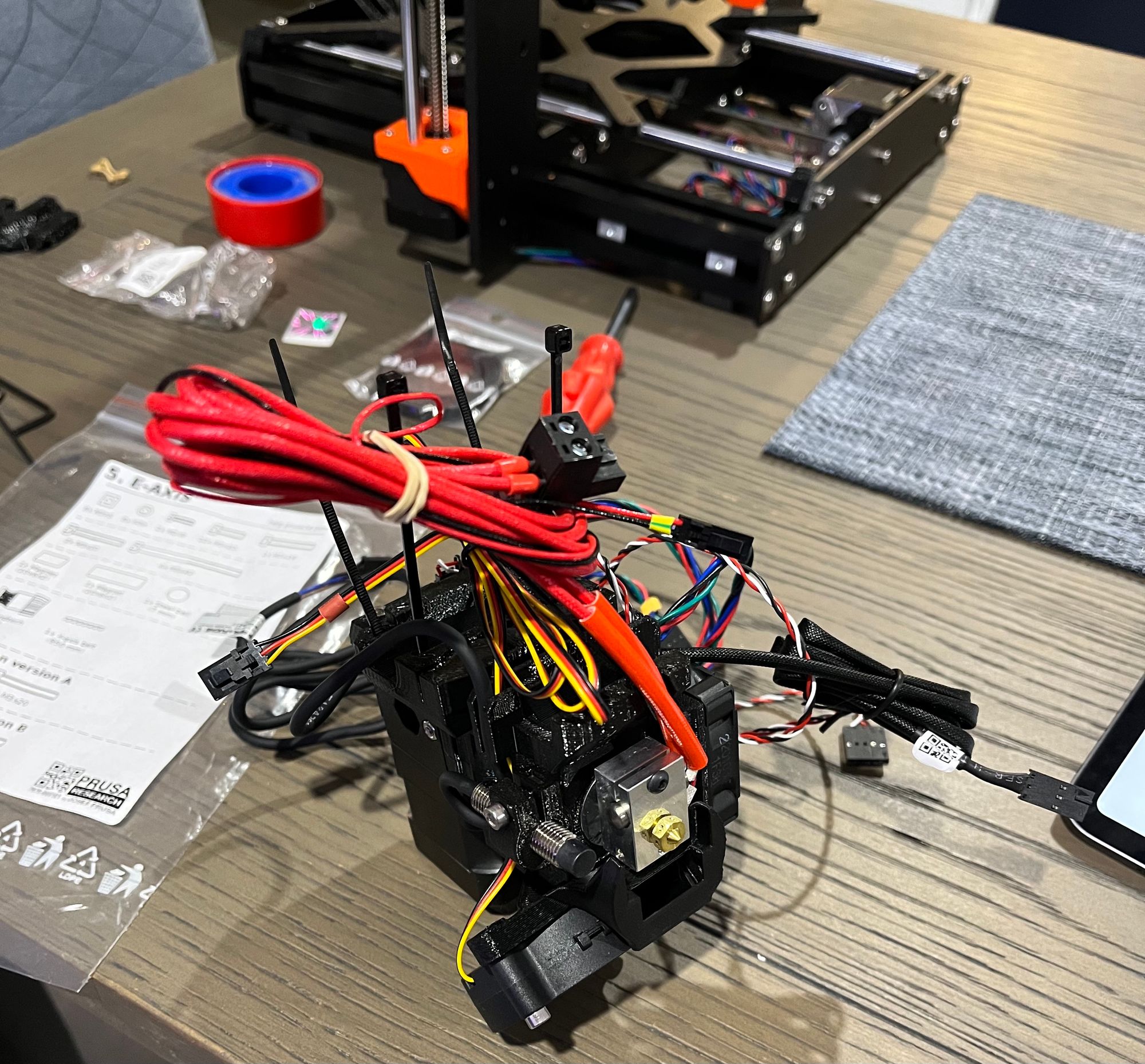
Cable management is a fine art. The opportunities for ruining everything got bigger and bigger as the hours rolled on.
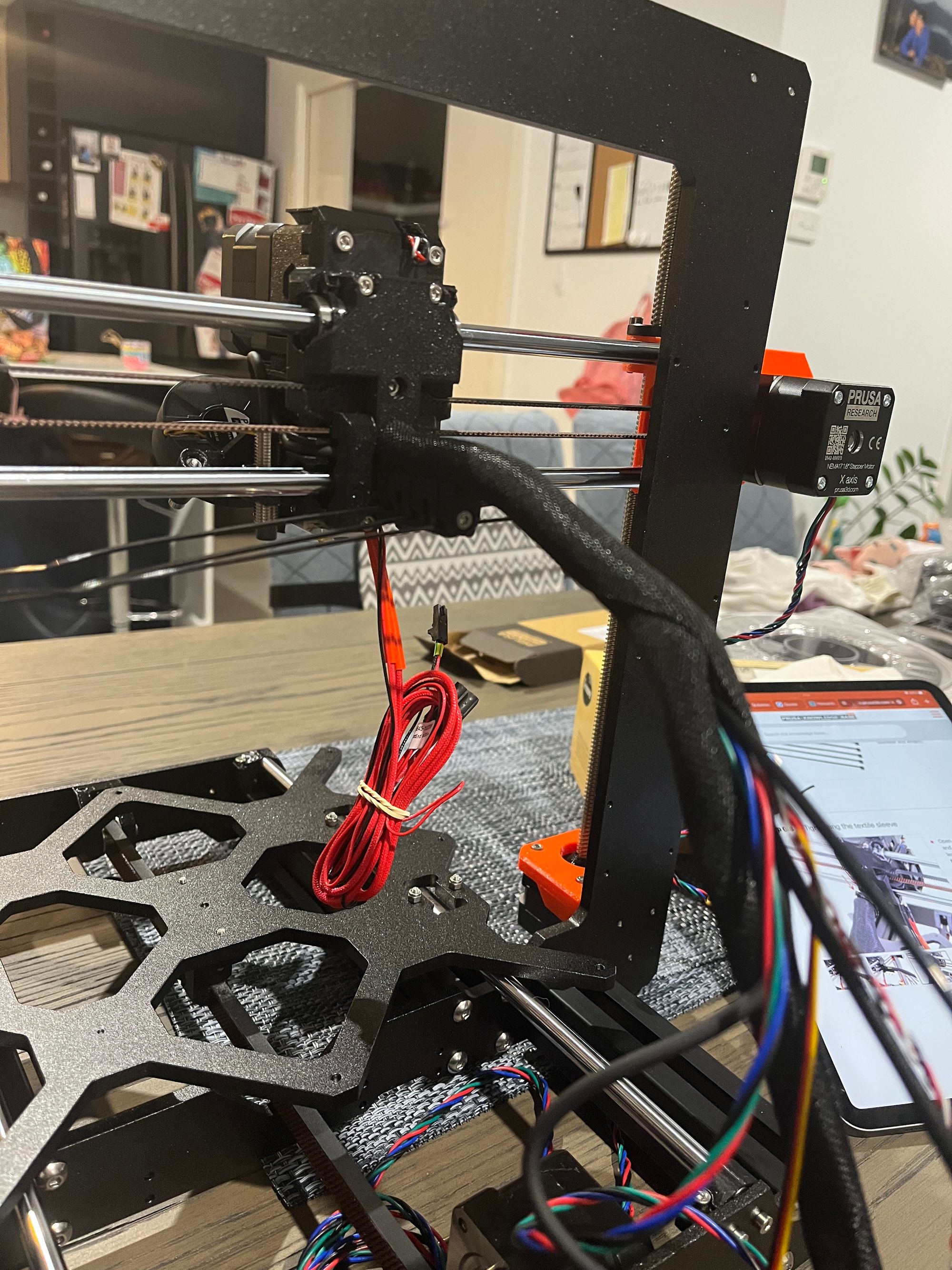
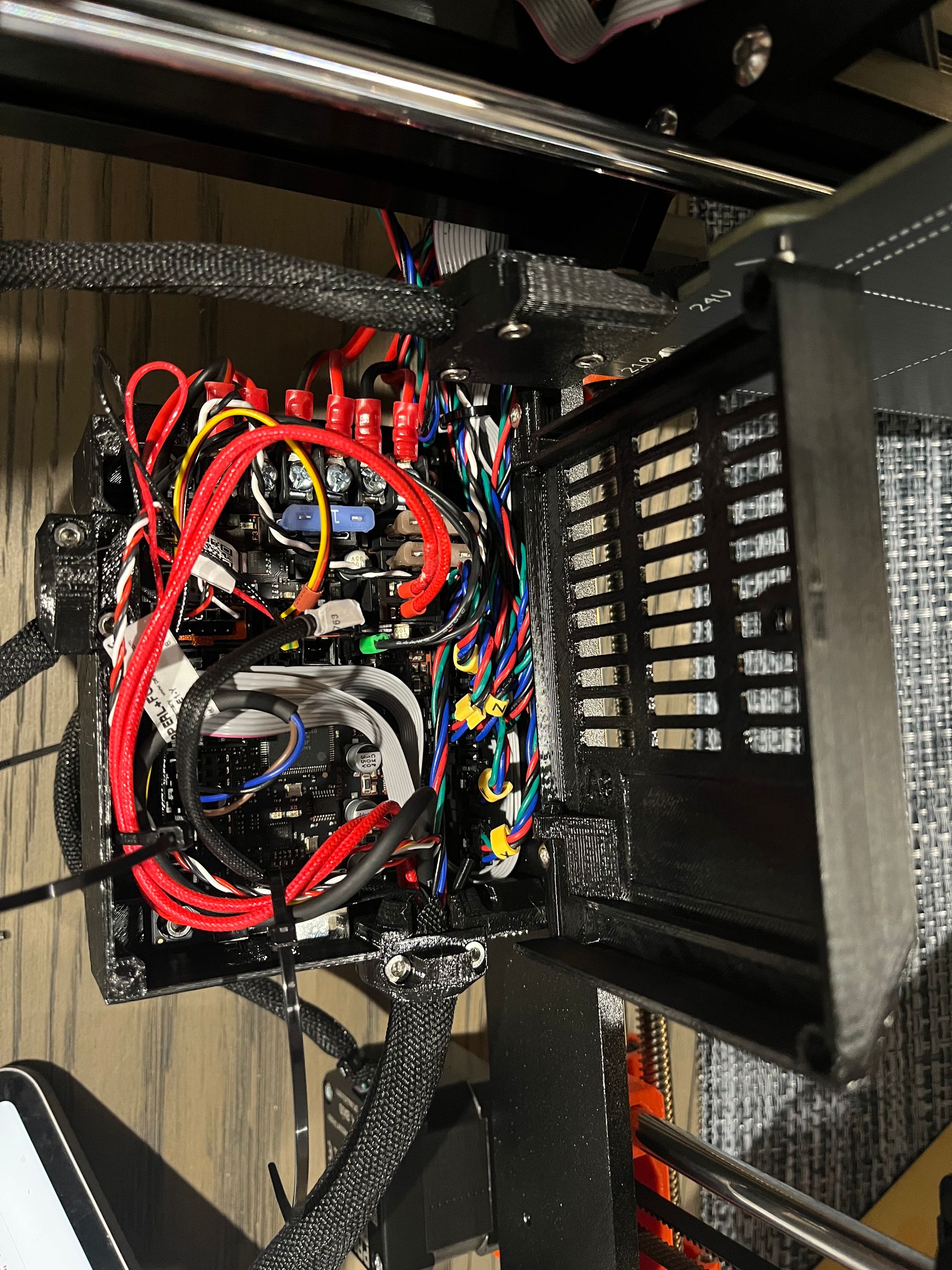
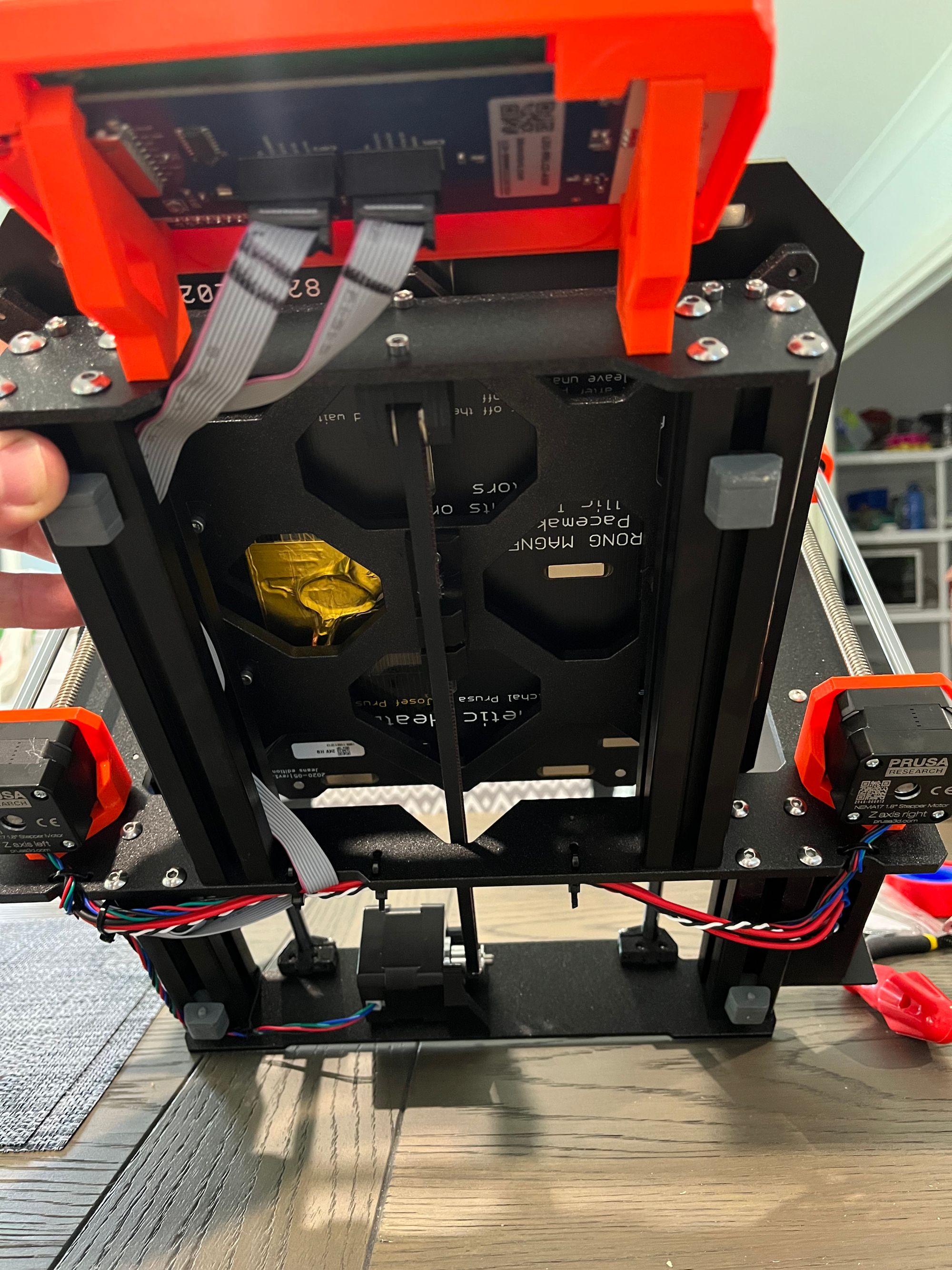
But I was one of the lucky ones ;-) After maybe 15 hours of tense concentration, this was an enjoyable moment.
Even the first customer left good feedback.
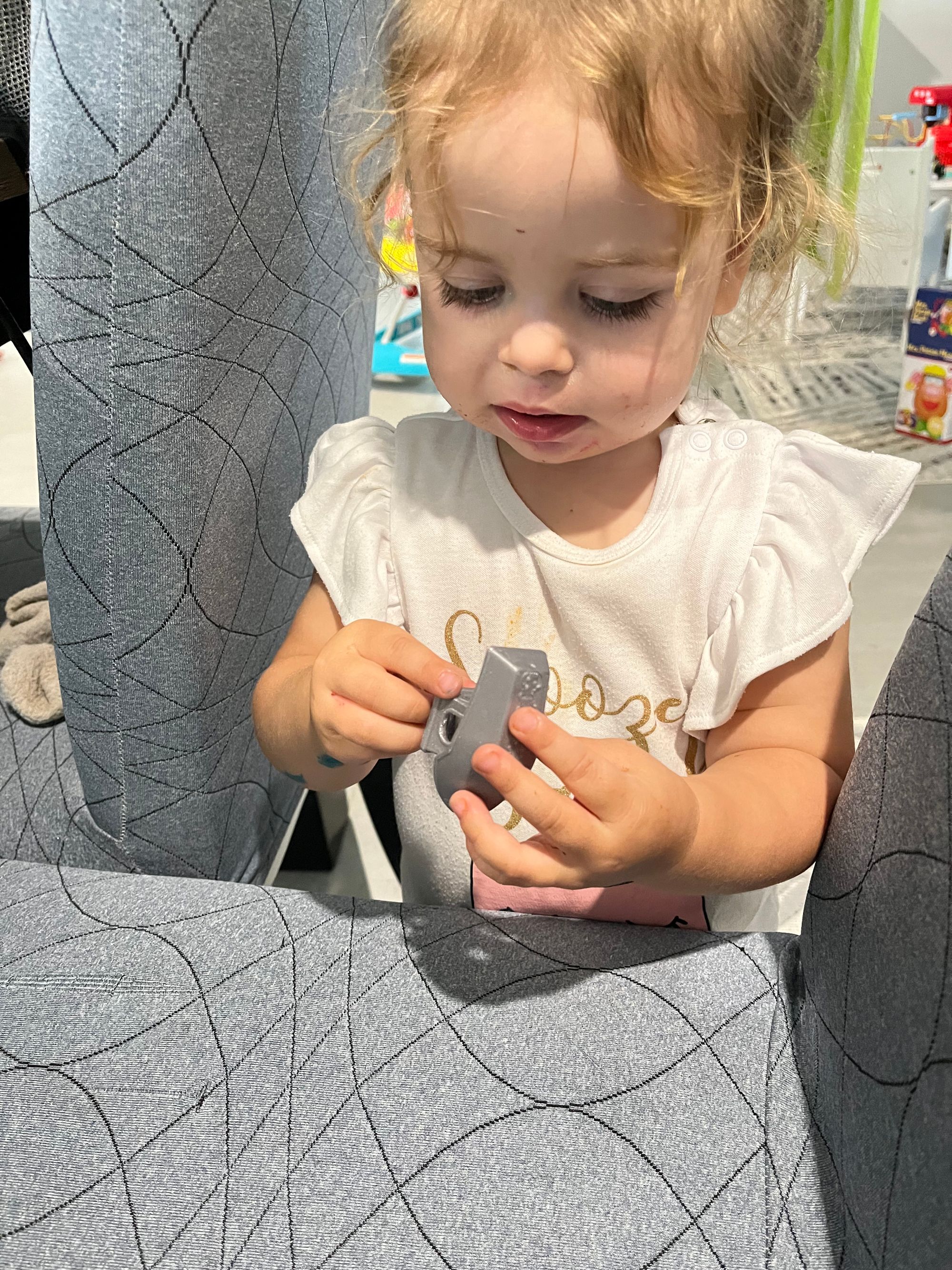
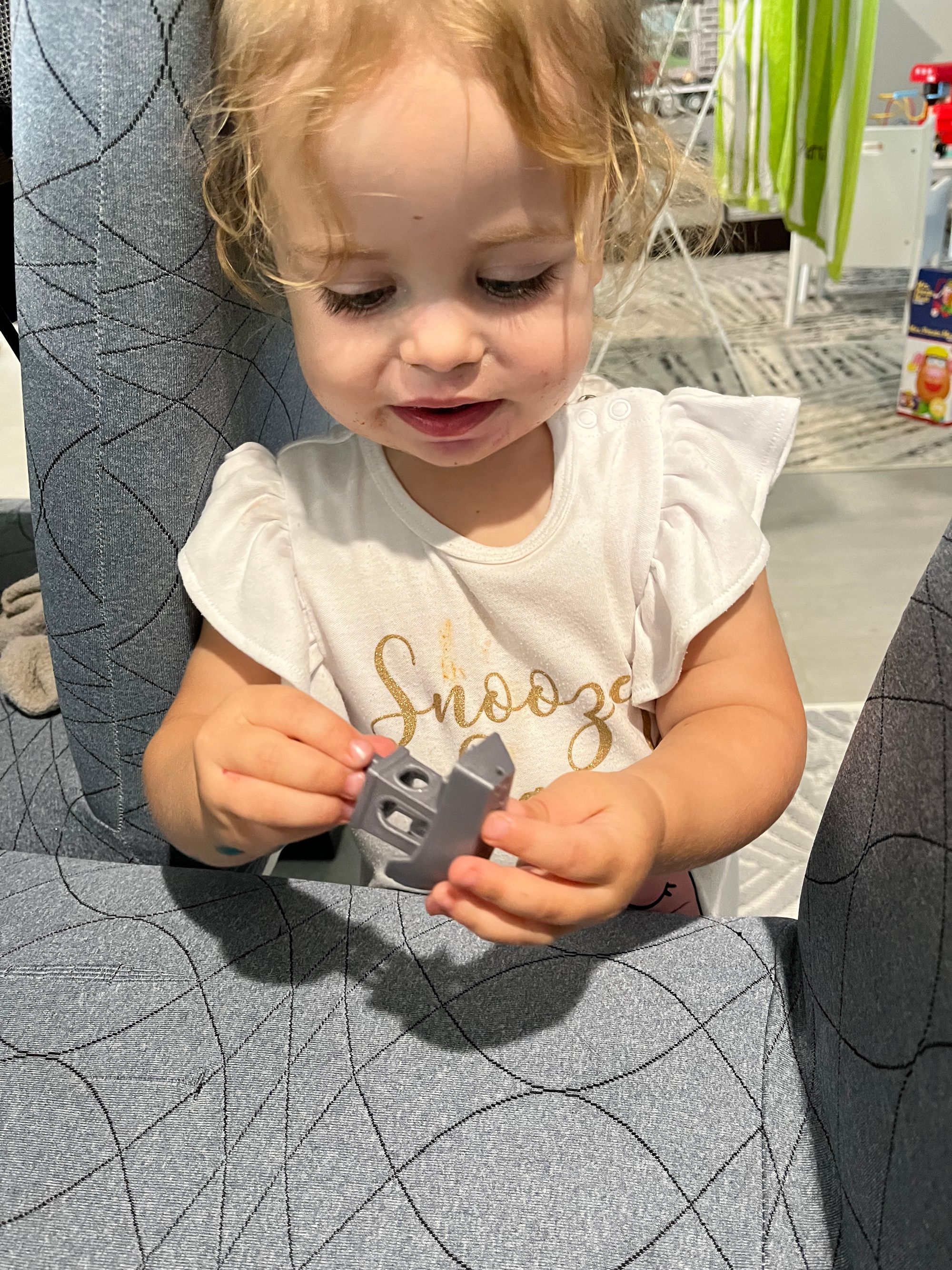
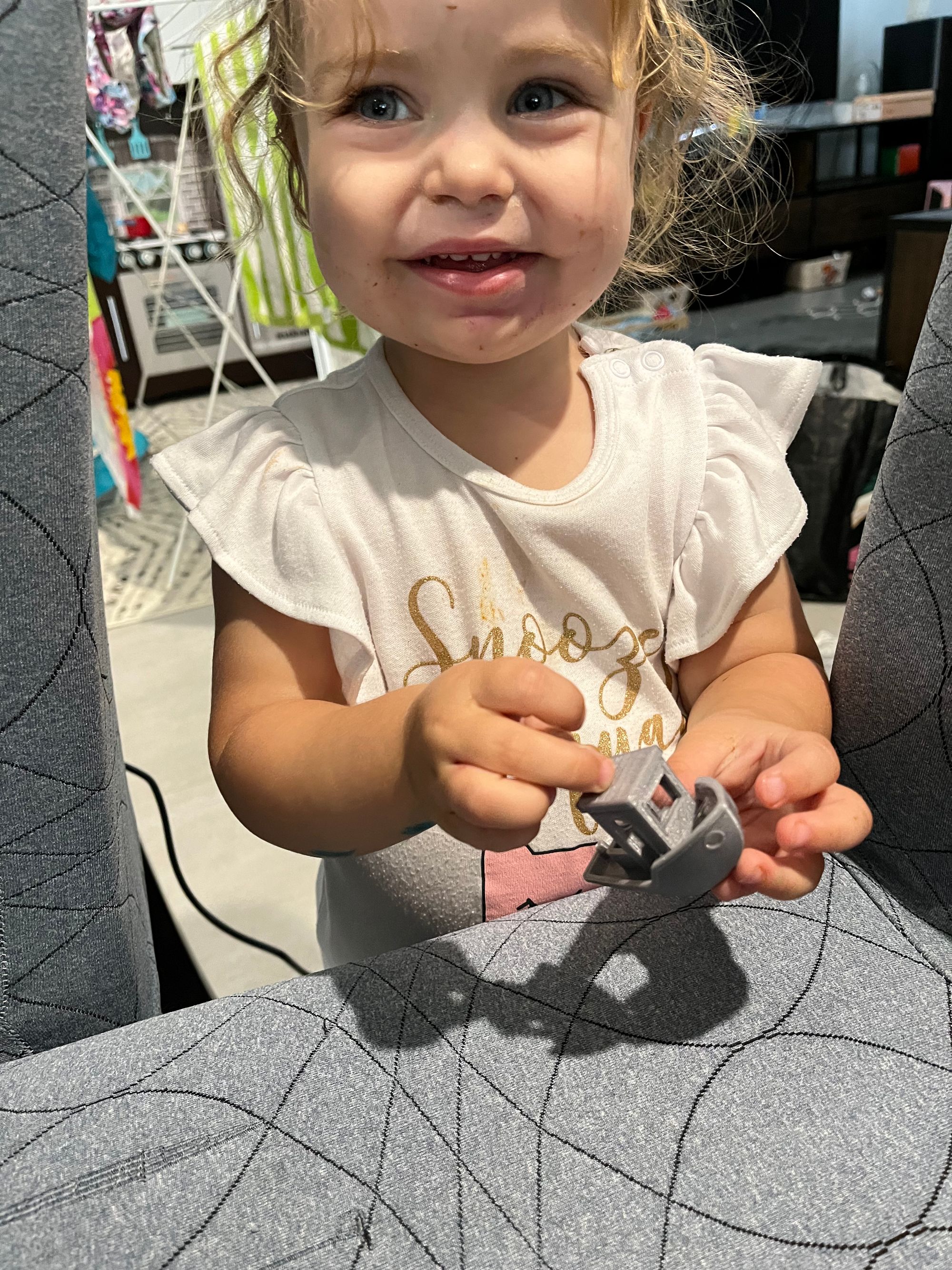